Recently, the Structural Thermodynamics and Micronanochemistry Group of the School of Chemistry and Chemical Engineering of Guangxi University has made a breakthrough in the development of electrocatalytic hydrogen production materials, and the research results have been published in the top international academic journal Advanced Materials under the title of “Size-Controllable High-Entropy Alloys Toward Stable Hydrogen Production at Industrial-Scale Current Densities”`. The first author of the paper is Wang Qian and Qin Yao, PhD students of the class of 2024 in the School of Chemistry and Chemical Engineering, and the corresponding authors are Zhao Shuangliang, professor of the School of Chemistry and Chemical Engineering, and Gui Zengxi, assistant professor of the School of Chemistry and Chemical Engineering, with Guangxi University as the sole corresponding unit.
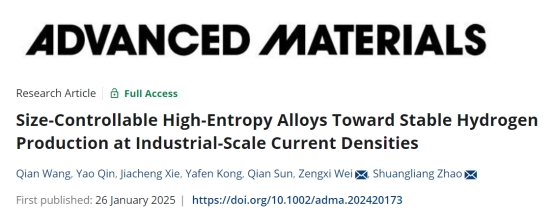
Catalyst is industrial MSG, a key raw material in chemical production, which plays an important role in improving production efficiency and reducing cost. Facing the bottlenecks in the current electrocatalytic hydrogen production technology, such as easy sintering of catalysts and deactivation of active sites, the research team proposed a design strategy for high-entropy alloys (HEAs) nanocatalysts based on the pentametals of palladium (Pd), platinum (Pt), ruthenium (Ru), rhodium (Rh), gold (Au), and other five-membered metals. Through the microreactor technology, the team realized the precise regulation of metal salt solution and reducing solvent under mild conditions (230 ℃), and successfully developed high entropy alloy nanoparticles with anti-sintering, anti-corrosion, and synergistic multiple active sites, and established a new method for size-controllable preparation.
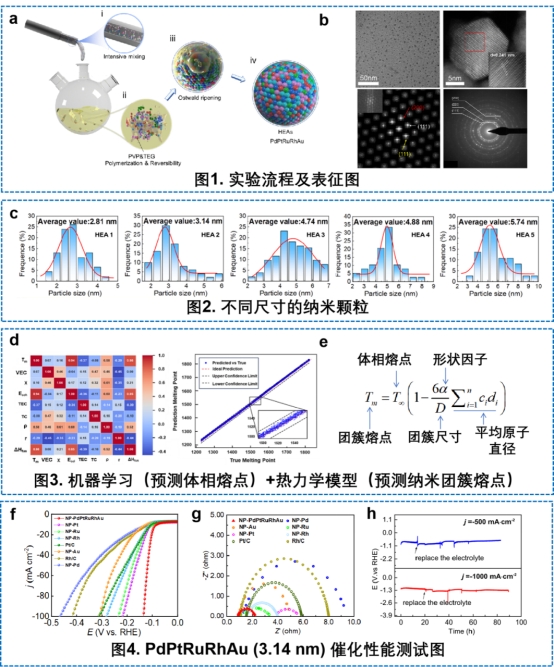
The team further sorted out the size effect of the high-entropy alloy nanocatalyst, and established a high-precision prediction model of the melting point of the nano-hyperentropic alloy by thermodynamic method and combined with machine learning; through the statistical analysis of the activity contribution of atoms on the surface of the nanocatalyst and the inter-atomic activity, the Pd-Au bridging site was identified as the main active site for hydrogen production of the high-entropy alloy catalyst, and the structure-efficacy relationship between size and hydrogen-producing performance of the nano-hyperentropic alloy catalyst was elucidated.
Combining experimental system and theoretical analysis, the research team finally developed a series of high-performance PdPtRuRhAu high-entropy alloy nanocatalysts. Application tests show that the high-entropy alloy catalyst with a size of 3.14 nm exhibits particularly excellent hydrogen production stability under acidic conditions, and its activity degradation is still negligible when it continues to produce hydrogen for more than 800 hours at a current density of -100 mA-cm-2; even at higher current densities of -500 and -1000 mA-cm-2, the catalyst also exhibits 100 hours of sustained stability without significant activity degradation. This work attempts to provide new ideas and research directions for the controllable design and application of high-entropy alloy materials in hydrogen production by coupling thermodynamic modeling, molecular simulation, machine learning, experimental characterization and microchannel reactors.
It is reported that this study was supported by the National Natural Science Foundation of China, the Youth Science Foundation, and the foundation of Guangxi.